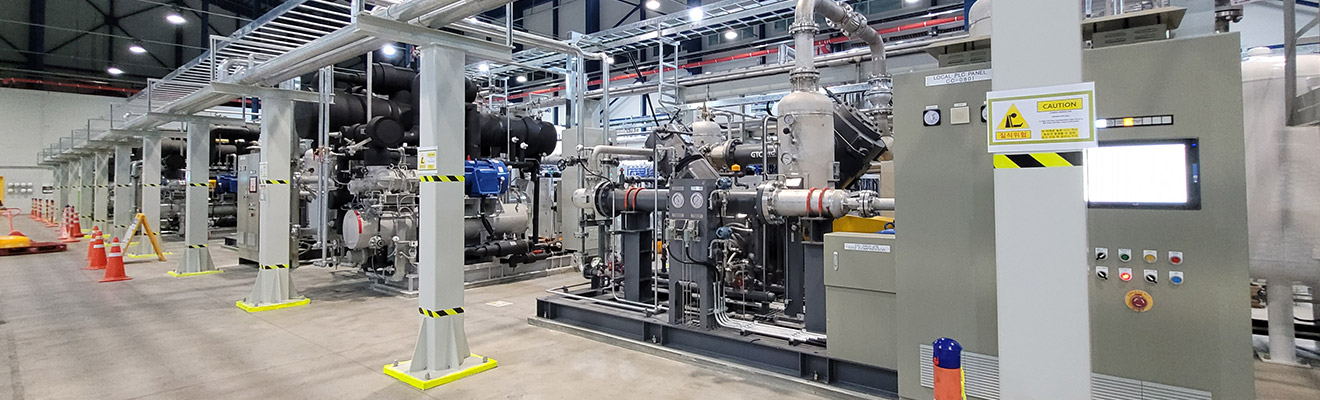
- The raw material of dry ice is LCO₂ (liquid carbon dioxide).
-
During the dry ice manufacturing process, more than 60% is released into the atmosphere.
CO₂ released into the atmosphere is recaptured, compressed and frozen to produce liquid carbon dioxide, and it is then put back into the dry ice manufacturing process, significantly reducing dry ice production costs.
Victex designs, manufactures, and supplies optimal recovery systems to meet customer needs, from small-capacity modular CO₂ recovery systems to mid- to large-capacity packaged unit-type CO₂ recovery systems.